atvise® SCADA
SCADA Software for Industry 4.0
The first HMI SCADA software built on Industry 4.0 fundamental basis:
Pure Web Technology and OPC UA
Industry 4.0
The SCADA software for industry 4.0: atvise®
Industrial processes automation with atvise® SCADA allows you to maximize the performance of your industrial plant, increasing productivity, efficiency, quality and profitability through 4 main features:

PURE WEB TECHNOLOGY
Pure SCADA web application
atvise® is the first professional HMI product that has been developed from scratch with web-standards like SVG (vector graphics) of the WWW Consortium (W3C). Only such technologies will be displayed and executed by all common web browsers without additional plug-ins, ActiveX, Java or Silverlight – today as well as in future.
No client installation necessary. You don’t have to set up, configure and maintain client software, and don’t worry about the operating system. Web browsers are available everywhere.
Responsive Webdesign. Different sizes of operating terminals of a plant, different displays of a control room, or mobile devices: content and interface adapt to the situation automatically.
OPC UA STANDARD
OPC UA in the core atvise®
When it comes to interoperability of systems, there is no alternative to OPC UA as the communications standard in industry 4.0.
Great advantages and benefits that, unlike other HMI SCADA industrial systems, are possible due to OPC UA is the second fundamental of atvise® SCADA web system.
This feature allows us to implement any new specification approved by the OPC Foundation.
Unlike traditional SCADA software, all internal components in atvise® are OPC UA nodes, ensuring the highest standardization level of your SCADA industrial communications.
Web SCADA software with OPC UA: Advantages and Benefits:
- Realtime SCADA data from PLCs, DCSs and systems from any vendor
- Historical data exchange – OPC UA HA client and server
- Vertical Object Oriented Engineering – atvise® goes further than object oriented engineering, by offering this feature directly through OPC UA
ENSURED ACCESIBILTY
SCADA software multiplatform
Install atvise® SCADA software in your server machine, both on Windows or Linux. Now you can choose the most convenient operating system for the installation of your SCADA software.
Compatible operating systems with atvise® SCADA software
Windows for a server machine shared with other corporative programs, Ubuntu to install your atvise® SCADA sooftware in the cloud and give remote access to your users, or Debian to install atvise® SCADA in a reduced PC with ARM architecture.
And what about the clients? Exactly! Clients are SCADA web applications that can run on Windows, Ubuntu, MAC, Android, iOS… on any operating system that supports web browsers.
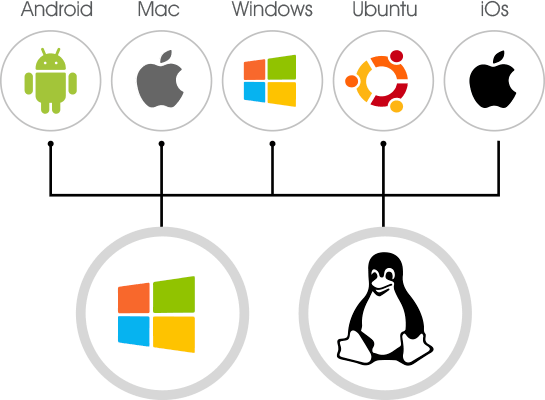
ENGINEERING TOOL
100% online engineering with atvise® Builder
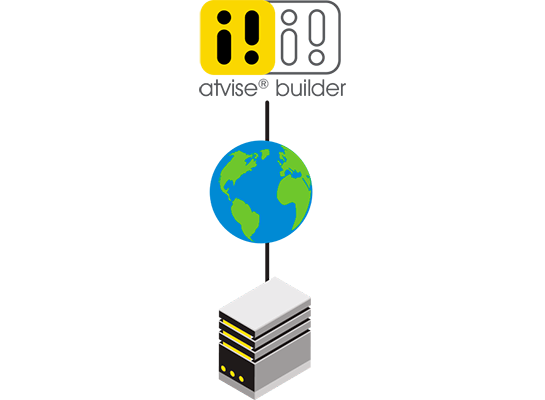
Atvise® SCADA software includes the engineering tool atvise® Builder by default. Access, design, edit, configure and make the whole commissioning of your automated process remotely. Avoid unnecessary travels, reduce costs of engineering hours, speed up project delivery terms, make modifications quickly and much more in the most secure way.
SCADA industrial development projects with atvise® Builder
Engineering tool atvise® Builder allows integrators or developers to create and modify projects from any location due to remote access through OPC UA.
With atvise® Builder, data acquisition and application design are easier, more secure and more efficient than ever.
SCADA Web atvise® adaptability
Intelligent monitoring and control
Automation of industrial processes
Any asset and managed process is monitored in real time, providing a complete view of the general state of the installation, also allowing specific decision-making based on data.
It is possible that, if you work in the industrial sector, you have used some software such as to remotely control an installation or automate processes, that is what a SCADA software does. In fact, it is the most efficient tool on the market to control, monitor, collect data, analyze it and generate reports with it.
In broader terms, SCADA software seek to improve the economic benefits of an industrial system through the optimization and control of all the processes that occur within the plant. Simply put, a SCADA is used to monitor and control equipment in an industrial process, including manufacturing, production, and development.
Composition of a SCADA software
As in most systems, we have two big players: software and hardware; and these will determine with more or less precision the final result.
Hardware
The hardware that a SCADA system requires is mainly the following:
PLCs or RTUs: They are connected to the machinery.
Servers: They collect all the data to form a database and apply the corresponding parameters on it.
A computer: From where the commands are executed.
A local network: Connects all systems to each other so that it works properly
Software
The SCADA software consists of a software program to provide real-time data, historical data, alarms, diagnostic data, and more. It also allows you to manage information such as scheduled maintenance procedures, logistics information, detailed schematics for a particular sensor or machine, and expert systems troubleshooting guides. This means that the operator can see a schematic representation of the plant being controlled.
Application of SCADA software in Industry 4.0
SCADA software are applied in industrial environments to maintain control over production processes, although in recent years their use has also been extended to sectors such as pharmaceuticals, agro-food, energy or water management.
Within the wide range of the industrial sector, it is in the following types of companies where SCADA software are being used the most:
- SCADA for petrochemical companies
- SCADA for telecommunications companies
- SCADA for machinery companies
- SCADA for energy production companies
This does not mean that they are the only ones where a SCADA software will work correctly, but they have more years of experience using these systems within their facilities. In fact, it can be applied to any type of industry, from water treatment to transportation.
Discover below, the benefits of adapting a SCADA Web system like atvise® to automate and manage your industrial processes:
SCADA software adaptable to any industry and sector
With more than 15 years of evolution, atvise® SCADA is implanted in all industrial sectors. Companies in industries such as Building Automation, Water Management, Energy, Manufacturing, Infrastructure, Oil & Gas or Transportation enjoy a modern and robust SCADA system.
Industria 4.0
atvise®: The most complete
SCADA software
Give the most power to your SCADA software through the available features included in
all atvise® licenses, even in the most basic one.
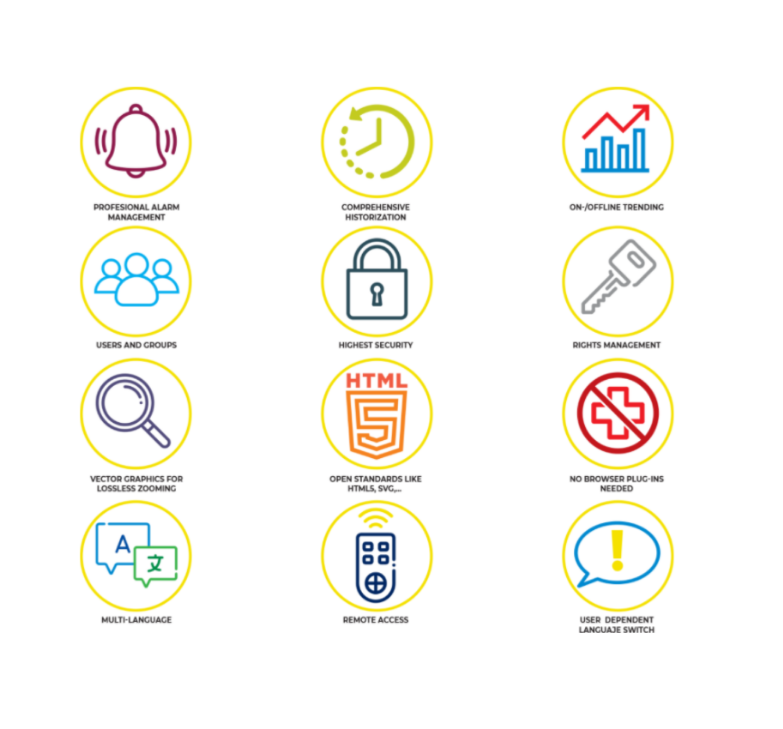
KNOWLEDGE AND TECHNICAL INFORMATION
atvise® SCADA Newsletter
More than 20.600 users are already getting our news!
Are you interested in technology oriented to Industry 4.0? Now you can upgrade your knowledge about atvise® SCADA software through our newsletter.
Subscribe to our newsletter and be the first to get known about the last news about intelligent industries!
atvise® SCADA Software: Industrial communication and process automation
We advise you free of charge on the best solution for your company or project in particular.
Solve your doubts and queries with the help of our team of specialists
in SCADA software systems. Talk later?
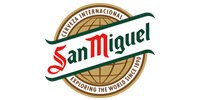
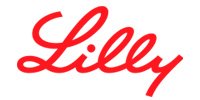
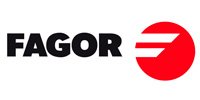
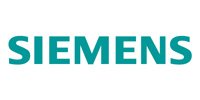

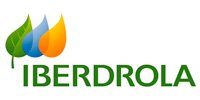
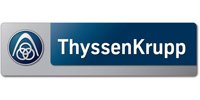
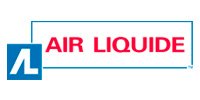
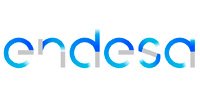
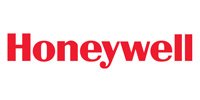
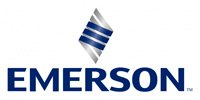
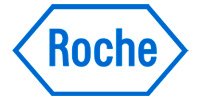
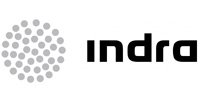
Web SCADA System: atvise
SCADA is an acronym that stands for “Supervisory Control and Data Acquisition,” known as “Data Acquisition and Supervisory Control.” SCADA is a software and hardware system used to control and monitor industrial and critical infrastructure processes, such as power generation, oil and gas production, water and gas distribution, traffic management, and building management, among others.
SCADA systems collect data through sensors and other devices in real-time and represent them in a graphical user interface for operators to monitor and control processes in real-time. They can also generate alerts and alarms when abnormal or hazardous conditions are detected.
The importance of SCADA systems applied to industrial processes
SCADA systems offer several advantages that make them very useful for the monitoring and control of industrial processes and critical infrastructures.
Moreover, they are significant in the industry because they can improve efficiency, safety, control, flexibility, and reduce production costs. This enables companies to be more competitive and profitable in an increasingly challenging production environment.
Some of the main advantages of implementing a SCADA system in the industry are:
- Increased efficiency: SCADA systems can help improve the efficiency of industrial processes by allowing operators to monitor and control processes in real-time. This means that operators can make more informed and faster decisions, thereby improving production efficiency and reducing downtime.
- Enhanced safety: SCADA systems can help improve the safety of industrial processes by allowing operators to monitor and control processes in real-time. This can help detect and prevent potential security issues before they occur.
- Cost reduction: SCADA systems can help reduce production costs as operators can detect and correct production issues more quickly, reducing downtime and minimizing material waste.
- Greater control: SCADA systems can provide greater control over industrial processes by allowing operators to monitor and control processes in real-time. This means that operators can make precise adjustments and take preventive measures to avoid problems before they occur.
- Greater flexibility: SCADA systems can provide greater flexibility in production, allowing operators to make quick and precise adjustments to processes in real-time. This means that operators can respond to changes in demand or production requirements more effectively.
Main Industrial Sectors Where SCADA is Used
SCADA systems are employed in a wide variety of industries of different typologies for the monitoring and control of critical processes. Some of the industries where these SCADA systems are used include:
- Energy Industry: in the generation, transmission, and distribution of electricity.
- Oil and Gas Industry: in the exploration, production, transportation, and refining of hydrocarbons.
- Water and Wastewater Industry: in the management and distribution of drinking water, wastewater treatment, and irrigation processes.
- Manufacturing Industry: in the monitoring and control of production in manufacturing plants.
- Transportation Industry: in the management of air, rail, and maritime traffic.
- Infrastructure: in the management of buildings, airports, bridges, dams, ports, and other critical infrastructure systems.
- Telecommunications Industry: in the management of telecommunications and data communication networks.
- Food and Beverage Industry: in the monitoring and control of food and beverage production processes.
- Pharmaceutical Industry: in the monitoring and control of the manufacturing processes of drugs and pharmaceutical products.
- Mining Industry: in the monitoring and control of the extraction and processing processes of minerals and metals.
Architecture and Elements of a SCADA System
SCADA (Supervisory Control and Data Acquisition) architecture refers to the structure or design of the control and monitoring system used to oversee and control industrial processes. SCADA architecture includes hardware, software, and communication protocols that work together to collect real-time data, process it, and present it to the end user. A typical SCADA system architecture is composed of the following components:
Data Acquisition Devices
These devices are responsible for collecting process data, such as temperature level, pressure, flow, among others.
Remote Terminal Unit (RTU)
This unit is responsible for collecting data from data acquisition devices and transmitting it to the central SCADA system.
Communication System
It is the means by which data is transmitted between devices and the central SCADA system. It can be through wired or wireless communications.
Data Server
This is the central component of the SCADA system, receiving, processing, and storing the data collected from RTU devices.
SCADA Software
This is the software that enables operators to monitor and control production processes in real-time.
User Interfaces
These are the devices through which operators interact with the SCADA system, such as monitors, touch screens, or user terminals.
SCADA architecture is crucial because it provides a solid framework for the design, implementation, and maintenance of a SCADA system, allowing users to fully leverage the benefits of an automated and real-time process control system.
Layers of Architectures in SCADA Systems
In general, a SCADA architecture consists of three main layers:
Data Acquisition Layer in a SCADA System
This layer is responsible for collecting data from sensors and devices in the field, such as temperature meters, limit switches, and control valves. Data is transmitted through standard communication protocols such as Modbus, OPC, DNP3, among others.
Data Processing Layer in SCADA Systems
This layer is responsible for processing the acquired data and transforming it into useful information. It includes a centralized or distributed SCADA server where data is stored, and SCADA software to process and present it in a user-friendly interface.
User Interface Layer in SCADA Systems
This layer serves as the interface between the user and the SCADA system. The information and data processed by the previous layer are presented in a graphical user interface (GUI) to allow the user to monitor and control the industrial process. The user interface may include graphics, tables, alarms, trends, among others.
In addition to these layers, a well-designed SCADA architecture may also include components such as firewalls, routers, switches, and other network devices to ensure communication security and reliability.
A well-designed SCADA architecture should be scalable, flexible, and reliable to adapt to the changing needs of industrial processes and provide high-quality monitoring and control.
Different Types of SCADA Systems
There are different types of SCADA systems, varying in their architecture, functionality, and capabilities. Below are descriptions of some common types of SCADA systems, though each type has its own advantages and disadvantages. The choice of the system type will depend on the specific application needs.
Centralized SCADA System
It is the most common type of SCADA system, where a client-server architecture is used to connect remote devices to a central control center. The control center oversees and controls remote processes through a communication network.
In a centralized SCADA system, all operations and controls are performed from a single control center, which can be located at a specific physical location or accessed through a communication network. This control center collects real-time data from various devices and sensors in the industrial process and displays it on a graphical user interface.
The system also allows operators in the control center to send commands and control devices in the field of operation, such as valves, motors, and other equipment. Additionally, centralized SCADA systems often have data storage and analysis capabilities, enabling operators to monitor system performance and make improvements.
In general, a centralized SCADA system is a useful tool for enhancing the efficiency and safety of industrial processes by providing centralized monitoring and control.
Advantages of a Centralized SCADA System
- Centralized Monitoring: In a centralized SCADA system, data is collected at a single point and stored on a central server. This allows centralized monitoring of processes and decision-making based on the collected data.
- Accessibility: Being centralized, data can be easily accessed from anywhere with a network connection. This allows operators to monitor and control the production process from any location, which can be especially useful for companies with facilities in multiple locations.
- Scalability: Being centralized, a SCADA system can be scaled to adapt to the changing needs of the company, such as the addition of new equipment or production processes.
- Lower Cost: A centralized SCADA system can be less expensive than a distributed system, as it may require less hardware and software and can be easier to maintain.
- Security: A centralized SCADA system can be more secure than a distributed system, as data is stored at a single point, making it easier to protect against security threats and attacks.
Decentralized SCADA System
In this type of system, monitoring and control are distributed across various remote locations instead of being centralized in a single control center. Each remote location has its own SCADA system, which communicates with other SCADA systems through a communication network.
In a decentralized SCADA system, each system component, such as sensors, actuators, and control units, is equipped with its own data acquisition and control unit. These units communicate with each other through a communication network, allowing the exchange of data and commands in real-time.
Each data acquisition and control unit is capable of collecting and analyzing data from its local environment and making decisions based on them. Additionally, data can be sent to a central location for analysis and decision-making at a higher level.
A decentralized SCADA system is useful in environments where components are geographically dispersed, and it is difficult or costly to connect them to a single control center. It can also be beneficial in environments where ensuring redundancy and fault tolerance is important, as the failure of one unit will not impact the entire system.
In general, a decentralized SCADA system allows for greater flexibility and scalability while enhancing the efficiency and safety of the industrial process.
Advantages of a Decentralized SCADA System
- Reduced Risk of Failures: In a decentralized SCADA system, different components are distributed across various points, reducing the risk of catastrophic failure. If one component fails, others can continue functioning to keep the production process running.
- Greater Flexibility: A decentralized SCADA system can be more flexible than a centralized system, as it can allow operators to monitor and control processes in remote or hard-to-reach locations. This can be especially useful for companies with operations in remote places or in the oil and gas industry, where processes are located in hazardous areas.
- Higher Data Processing Capacity: In a decentralized SCADA system, data processing occurs on devices in the field rather than on a centralized server. This can enable higher data processing capacity and faster processing, which can be particularly useful for processes requiring a quick response.
- Lower Latency: Being distributed, a decentralized SCADA system can allow lower latency in data transmission and a faster response time, which can be crucial for processes requiring swift responses.
- Lower Network Costs: Being distributed, a decentralized SCADA system may require less bandwidth and, therefore, can be more cost-effective in terms of network costs.
In general, a decentralized SCADA system can be a good choice for companies seeking a flexible and fault-resistant solution for monitoring and controlling processes in remote or hard-to-reach locations or for processes that require a quick response.
Cloud-based SCADA System
This type of system utilizes cloud services to store and process SCADA data. Cloud architecture allows users to access data and control processes from anywhere with an internet connection.
Instead of using a physical control center, data is transmitted through a communication network to a centralized cloud platform, where it is stored, analyzed, and presented in a user interface.
In a cloud-based SCADA system, data can be collected through sensors and monitoring devices located in different geographical locations and connected through a network. This data can be securely transmitted over the Internet to the centralized cloud platform where it is stored and processed.
In addition to providing access to real-time monitoring and control data from anywhere and at any time through an internet connection, cloud-based SCADA systems may offer other advantages such as scalable and secure storage of large amounts of data, the ability to perform advanced analytics, and integration with other cloud applications.
However, there are also some challenges with cloud-based SCADA systems, such as data security during transmission and storage, as well as the need for a reliable and high-speed internet connection. Additionally, infrastructure and cloud connectivity costs can be a significant factor in the decision to implement a cloud-based SCADA system.
Advantages of a Cloud-based SCADA System
- Accessibility: Being hosted in the cloud, a cloud-based SCADA system can be accessible from anywhere with an internet connection. This allows operators to monitor and control production processes from any location, which can be especially useful for companies with facilities in multiple locations.
- Scalability: A cloud-based SCADA system can be easily scaled to adapt to the changing needs of the company, as it does not require additional physical infrastructure to grow.
- Cost Reduction: A cloud-based SCADA system can be more economical than a local system, as it does not require investment in additional physical infrastructure, such as servers and network equipment.
- Increased Security: Cloud service providers often have advanced data security and protection measures, which can enhance data security and reduce vulnerability to cyber attacks.
- Ease of Integration: A cloud-based SCADA system can be easily integrated with other systems in the company, such as inventory management systems or Enterprise Resource Planning (ERP) systems.
In general, a cloud-based SCADA system can be a good option for companies seeking a scalable, accessible, secure, and cost-effective process monitoring and control solution. Additionally, it may also be suitable for companies looking for a solution that easily integrates with other business solutions.
Distributed SCADA System
In this type of system, monitoring and control are distributed across multiple servers that communicate with each other through a communication network. Each server can monitor and control a specific part of the process.
In a distributed SCADA system, each control system is responsible for a part of the industrial process, and each has its own set of sensors, actuators, and control units. These systems communicate with each other through a communication network, allowing the exchange of data and commands in real-time.
Each control center can make independent decisions based on the data and information it collects and can provide a detailed view of its section of the process. Additionally, control centers can collaborate to make higher-level decisions and optimize the overall system performance.
Instead of relying on a single control center, distributed control systems use multiple control centers in different locations to collect data, monitor the process, and make decisions.
A distributed SCADA system is beneficial in environments where the industrial process is complex and extensive, and where it is necessary to collect and analyze large amounts of data. Furthermore, distributed control systems offer increased redundancy and fault tolerance, ensuring continuous system availability.
In general, a distributed SCADA system allows for greater flexibility and scalability while enhancing the efficiency and safety of the industrial process.
Advantages of a Distributed SCADA System
- Greater Reliability: Being distributed, a distributed SCADA system can provide greater reliability and redundancy. If one component fails, other components can continue functioning, reducing the possibility of catastrophic failure.
- Flexibility in Implementation: A distributed SCADA system can be more flexible in terms of implementation, as it can be customized to meet the specific needs of the company and the production process.
- Higher Processing Capacity: By distributing processing load across multiple devices, a distributed SCADA system can offer higher processing capacity, which can be beneficial for processes requiring a quick response or handling large amounts of data.
- Reduced Latency: Being distributed, a distributed SCADA system can provide lower latency in data transmission and faster response time, which can be important for processes requiring a quick response.
- Increased Security: Being distributed, a distributed SCADA system can provide higher security, as data is not centralized at a single point of failure. Additionally, distributed SCADA systems can be more challenging for cybercriminals to attack, as they cannot compromise all systems at once.
In general, a distributed SCADA system can be a good option for companies seeking a solution that provides greater reliability and redundancy, higher processing capacity, and increased security. It may also be suitable for companies looking for a process monitoring and control solution that can be customized to meet the specific needs of the company and the production process.
Single Operator SCADA System
A Single Operator SCADA (Supervisory Control and Data Acquisition) system is a type of control and supervision system where a single person is responsible for controlling and supervising the entire industrial process. In this type of system, a sole operator is in charge of monitoring and controlling industrial processes through a centralized user interface.
In a Single Operator SCADA system, all control and supervision operations are performed from a single location, where the operator can view and control all processes in real-time. The operator can monitor system data and alerts, make adjustments, and issue commands through a single user interface.
This type of system is suitable for smaller and simpler industrial processes where detailed control and monitoring are not necessary. Additionally, it may be a more economical option, as there is no need for multiple operators to monitor different parts of the industrial process.
However, there are also some challenges with a Single Operator SCADA system. In particular, information overload can be an issue if the industrial process is complex and requires constant attention. Additionally, the lack of redundancy can be a problem if the single operator is unavailable or experiences a technical failure.
In summary, a Single Operator SCADA system is typically used in situations where only one operator is needed to supervise and control a process. The user interface is simplified to make it user-friendly for an operator without extensive experience.
Advantages of a Single Operator SCADA System
- Simplicity: A Single Operator SCADA system is simple and easy to use, designed to be operated by a single user.
- Lower Cost: A Single Operator SCADA system can be less expensive than larger and more complex SCADA systems, as it does not require as much hardware and software.
- Increased Efficiency: A Single Operator SCADA system can provide greater efficiency to the production process, as the operator can monitor and control the entire process without having to communicate with other operators or departments.
- Greater Flexibility: A Single Operator SCADA system can offer greater flexibility, as the operator can adjust the process in real-time as needed, which can be useful for processes requiring a quick response.
- Shorter Training Time: A Single Operator SCADA system can be easier to learn and use, reducing the training time required for operators.
En general, a single-operator SCADA system can be a good option for companies seeking a simple, efficient, and cost-effective solution for process monitoring and control. It may also be suitable for smaller production processes that do not require a larger and more complex SCADA system.
Web-based SCADA System
A Web-based SCADA (Supervisory Control and Data Acquisition) system is a type of control and monitoring system that utilizes web technologies to provide remote access to data and monitoring and control functionality. In this type of system, data and control functionality are stored on a web server and accessed through a web interface, which can be accessible from any device with an internet connection.
In a web-based SCADA system, the user interface is presented through a web browser, allowing for an intuitive and user-friendly interface. Users can access monitoring and control data, make adjustments, and issue commands through the web user interface from anywhere with an internet connection.
This type of system runs on a web browser and communicates with field devices through a communication network. The user interface is accessible from any internet-connected device, providing greater flexibility and mobility.
Additionally, a web-based SCADA system also allows for greater flexibility in terms of scalability and geographical distribution. Data can be collected through sensors and monitoring devices located in different geographical locations and connected through a network. This data can be securely transmitted over the Internet to the centralized web server, where it is stored and processed.
A web-based SCADA system can offer many advantages, such as remote access to real-time monitoring and control data, an easy-to-use user interface, scalability, and flexibility to adapt to changing industrial process requirements. However, it is also important to consider data security in transit and storage, as well as the need for a reliable and high-speed internet connection.
In general, a web-based SCADA system is a modern and advanced solution for monitoring and controlling industrial processes and may be suitable for companies and organizations requiring remote access to data and monitoring and control functionality.
Advantages of a SCADA Web System
- Accessibility: A SCADA web system is accessible from anywhere through an internet connection. This means operators can monitor and control the production process from any location, which can be useful for companies with multiple locations or for operators who need to access the system outside the plant.
- Data Sharing: A SCADA web system allows easy sharing of data among different departments or users. This can enhance collaboration and efficiency within the company.
- Lower Cost: A SCADA web system can be less expensive than a traditional SCADA system, as it may require less hardware and software. Additionally, using a cloud-based platform can eliminate the need for costly local infrastructure.
- Automatic Software Updates: A SCADA web system can have automatic software updates, meaning users don’t have to worry about manually updating the software. This can save time and reduce errors.
- Improves Decision-Making: A SCADA web system can provide real-time information and analysis tools, improving decision-making and helping identify issues before they occur.
In general, a SCADA web system can be a good choice for companies seeking a monitoring and process control solution that is accessible from anywhere, easy to share data, cost-effective, and has automatic software updates. It may also be suitable for companies looking for a solution that enables them to make informed decisions based on real-time data.